The deepest mining pit in Poland, the GG-1 shaft in Kwielice, is 1348 meters and belongs to KGHM Polska Miedź S.A. June 14, 2023. was an important day in the company’s history. It was on this day that the technical nailing took place, i.e. the connection of the shaft to the KGHM O/ZG Rudna mine.
The commissioning of the GG-1 shaft will enable the exploitation of new copper deposits located in the Glogow Głęboki Industrial area. The contractor for this key KGHM investment is a KGHM Group company, Przedsiębiorstwo Budowy Kopalń PeBeKa S.A., which specializes in underground construction. It is the 31st. shaft built by PeBeKa in the Copper Belt.
UNIQUE SOLUTION
Sinking the shaft is only part of an investment to enable KGHM PM S.A. to continue mining copper ore deposits. The descent of mining to lower and lower regions is related to the successively increasing temperature of the rock mass. Beyond 1,000 meters, the primary temperature of the rock begins to approach 50oC, and the combustion machinery operating in the mine further increases it. An additional complicating factor is high humidity. The increasing distance of the “faces” where mining takes place from the intake and outbound shafts makes it necessary to transport workers by sidewalks over increasing distances. Clean air supplied through the inhalation shafts underground heats up quickly and needs to be cooled to a temperature at which human work is legally possible. All this makes the provision of an efficient air cooling system inside the mine, a necessity. At such depths of mining, solutions using bench or face air conditioning become ineffective. The answer to this challenge is the construction of a central air conditioning system with chilled water generation, i.e. water at a temperature of approx. 1.5oCin surface air-conditioning stations such as PSK.
The surface air conditioning station at the GG-1 shaft was designed with a trigeneration system. This means that chilled water, which is a source of cooling, hot water, which is a “waste” in the power generation process, and electricity are generated simultaneously. The technological system makes use of “waste heat” generated during the operation of gas engines, which, depending on the needs, is transformed with the help of absorption units into cold (chilled water) or distributed by means of heating nodes. Currently, a heating node is being put into operation for heating the inlet air to the GG-1 shaft, while in the future, among other things, it will be connected. administrative and social building, construction of which is scheduled to begin in the next two years. Thus, all types of energy accompanying the technological process are used. The station’s current cooling capacity is 33 MW, but an expansion to 40 MW is planned. The two cogeneration systems installed at PSK are capable of covering the electricity needs of the station itself, the glazing facilities, as well as the administrative and social buildings.
Controlling the entire process and controlling the parameters is automatic and unmanned (only under the supervision of employees). It should be mentioned that the PSK produces chilled water at temperatures close to 1.5oC, which poses a risk of freezing the plant and requires advanced automation to ensure the safety of the process.
Technical data
- cooling capacity: 33 MW.
- chilled water flow: 1400m3/h,
- parameters of chilled water supply to the three-chamber feeder: 1,5°C,
- II-stage chilled water cooling system using chillers,
- 10 fan cooling towers operating in full automation,
- A free-cooling system of 15 WMt.
THE COLD “COMES DOWN” TO THE FINE
The ice water generated at the Surface Air Conditioning Station must be transported inside the mine. The PSK built at GG-1 shaft supplies cooling to two mines, KRG Rudna and KRG Polkowice-Sieroszowice. Chilled water is supplied from the PSK via pipelines running to wells drilled directly into the ground. Location of three-chamber feeders on the pos. 1250 m, near the outlets of the boreholes makes it possible to limit the length and extent of underground networks of chilled water pipelines. This solution makes it possible to reduce the loss of cooling energy by 50%, as well as to avoid losses in ventilation systems.
The use of trigeneration technology and modern automation makes the PSK a unique facility of its kind, not only in the Legnica-Glogów Copper Belt, but also on a global scale. It is also worth noting that the investment makes it possible to obtain energy and cooling in an environmentally friendly way, without emitting harmful dust into the atmosphere.
Plans to mine copper at a depth of more than 1,000 meters were made at KGHM more than 20 years ago, and shaft sinking began on December 11, 2013. The Kwielica shaft is a ventilation, inhalation shaft that will be used to transport people and materials to the mine. A frozen rock mass technique was used during sinking. This is a pioneering method that PeBeKa has been perfecting for many years. In preparation for freezing the rock mass, 40 freezing holes with a diameter of 16 m were drilled and connected into a freezing system with a freezing aggregate station. The brine, cooled to the right temperature (-20 – – 40oC), circulating in the holes, freezes the rock mass to a depth of 700 meters. This method makes it possible to protect the shaft from groundwater flooding and allow safe penetration through loose rock mass layers composed of sands, clays, gravels, etc. In the case of the GG-1 shaft, whose depth exceeds 1,300 meters, one can speak of an exceptionally deep freezing zone. Currently, the elements needed for the shaft sinking stage are being dismantled and prepared for equipping with the necessary installations and equipment for the target period.
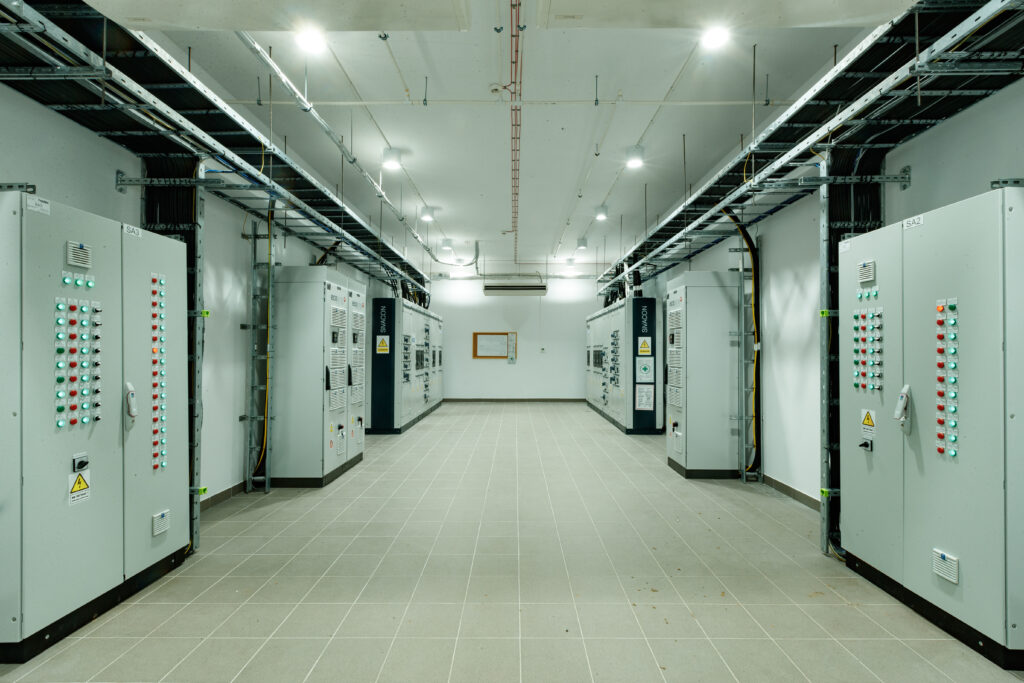
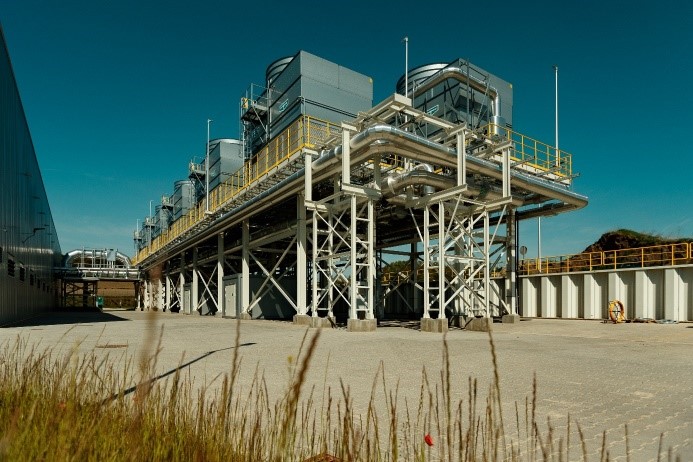
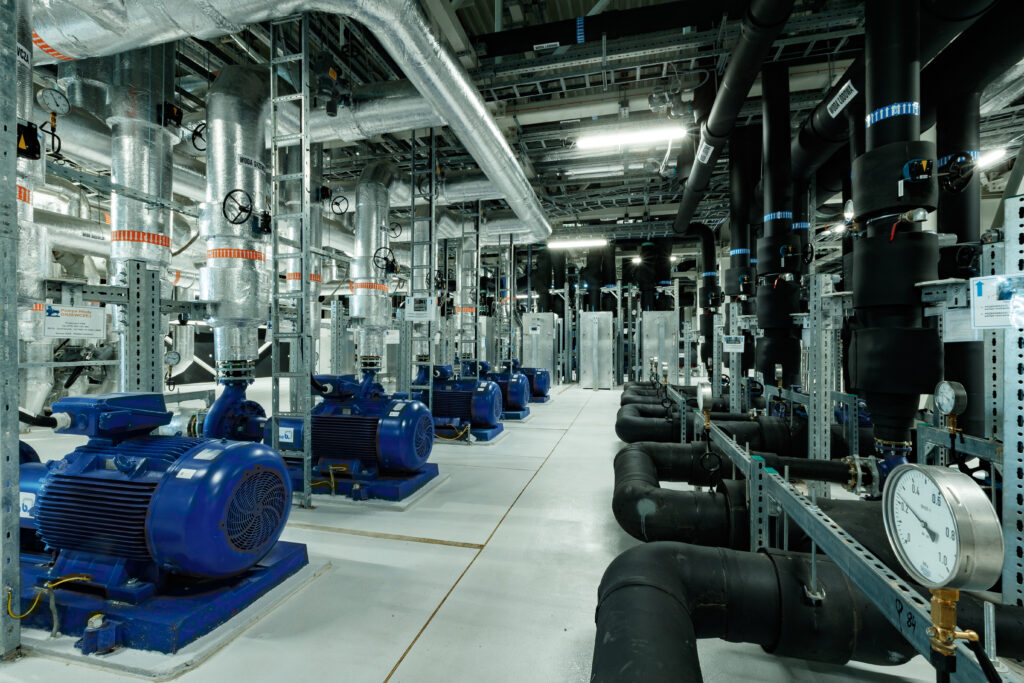
Elaborated. mj, photos: PeBeKa